Our Story
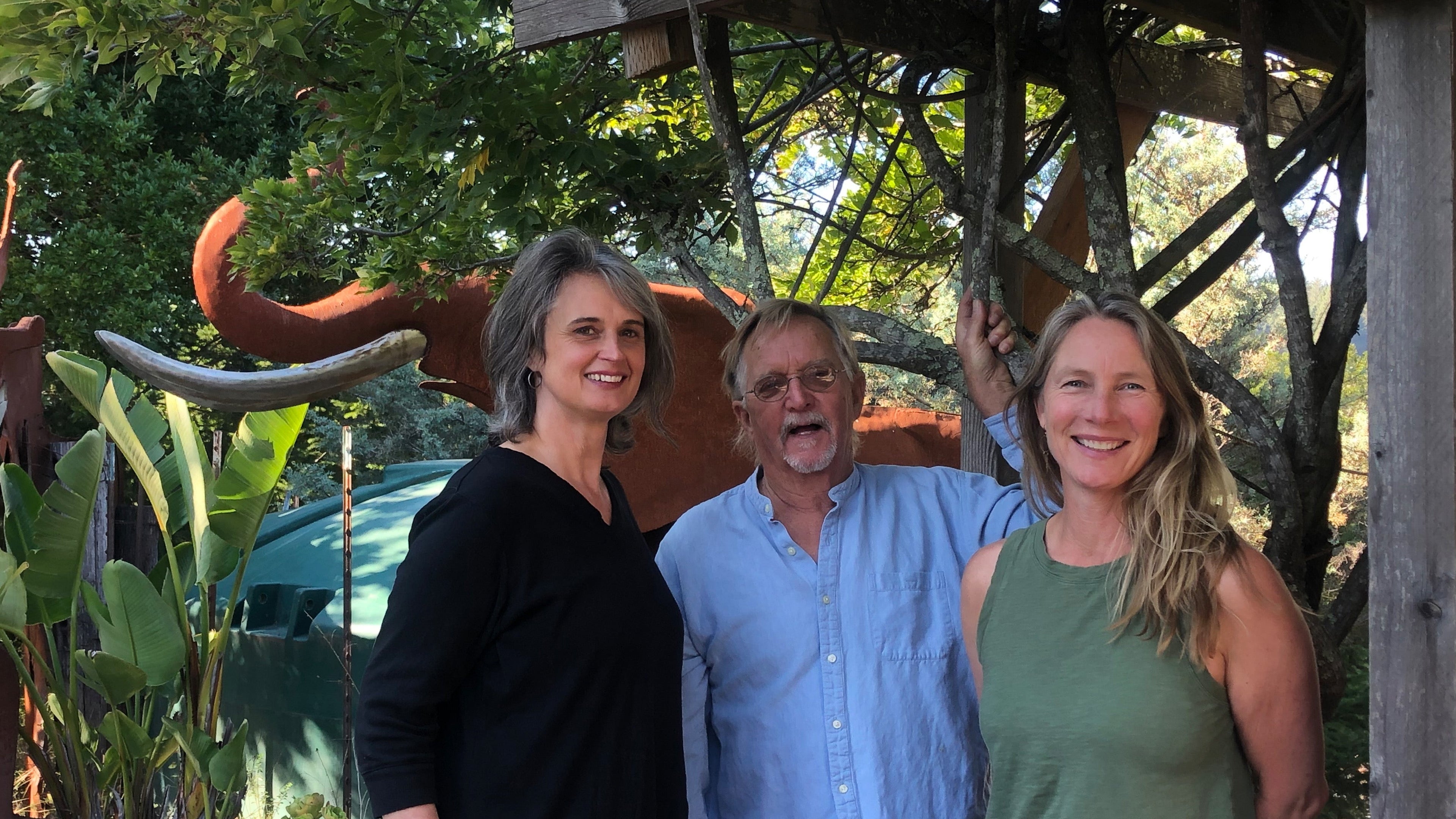
The Butterfly Effect
Back in 2003 at a solar energy festival, legendary activist julia butterfly hill holding up single use plastic water bottle in one hand and a stainless Indian lunchbox 'tiffin' in the other, asked something like "why doesn't someone make this - out of this?" Inventor and artist Robert Seals picked up what ms. butterfly was putting down and went on to create the world’s first stainless steel water bottle company, with a little help from a former plastic Nalgene bottle fanatic, Kathy Staychock. The stainless bottles caught on like crazy, igniting public awareness about the dangers of BPA and fueling a global shift toward stainless steel reusable bottles. What began as a niche solution for clean hydration rapidly grew into a multi-billion dollar industry—but with one major flaw..
Rewind. There’s a bit of a backstory. Twenty years before julia’s call out, Robert welded stainless steel tanks for the dairy industry. He manually buffed and polished the inside of tanks to reach a smooth, shiny finish to meet stringent FDA standards. The tedious process was called passivation – key to removing nooks and crannies that harbor bacteria and spoil milk. The passivation process naturally brings the chrome in stainless steel to the surface, acting as a seal preventing cross-contamination between the other corrosive metal components and acidic liquids. Robert later drew on this welding experience to build a stainless steel water bottle prototype.
When the first sample bottles arrived, Robert questioned the dull interior finish and was told that electropolishing was the new (cheaper) industry standard for passivation. Robert was not convinced and demanded a sticker on each bottle stating ‘for water only’ because he knew this relatively rough interior would continue to react with acidic beverages unless it was mirror-finished to achieve a chromium oxide layer. Chromium is the stable component in stainless steel that makes it “stainless” - as long as it’s brought to the surface through certain techniques. The other elements in stainless steel are reactive or corrosive. Robert made peace that these reusable bottles were for water, which is pH neutral and wouldn’t trigger a corrosive reaction.

Fast forward..
For two decades, the stainless reusable bottle industry evolved with exterior bells and whistles (colors, sizes, shapes, straws, even apps). Surprisingly, the interior standard finish has not changed one bit for over 20 years - even though stainless tumblers, commuter mugs and bottles are marketed for daily acidic drinks like coffee, smoothies, protein shakes, beer, wine and cocktails.
Turns out acidic liquids react with stainless steel IF it’s finished improperly - like it has been ever since water bottles morphed into beverage containers.

WHAT'S INSIDE YOUR BOTTLE? Good question!
We got the band back together to call out what you probably suspected: your cupboard full of stainless bottles, tumblers and thermoses are leaching metals (causing a metallic taste) into beverages while harboring bacteria & mold (causing that funky smell).
It's time for an update.
We have the goods. Beverage Safe is a woman-owned company that donates over a third of proceeds to local nonprofits. The butterfly effect is still rippling..